Dry granulation has been known for decades.
The main benefit is a lower cost of operation compared to wet granulation. New solutions now exist to easily test dry granulation on small scale early in the development process which was
not feasible before.
WHY IS DRY GRANULATION SO
POPULAR THESE DAYS?
Granulation of pharmaceutical
powder is often required to
prevent segregation of the Active
Pharmaceutical Ingredient (API). It
also enhances the blend flowability,
which is critical to ensure consistent
tablet mass (weight) on rotary tablet
presses. It is also used when API is
heat and/or moisture sensitive and
therefore wet granulation should be
avoided. But most interestingly, it is
also a real continuous granulation
process, which is a big trend these
days. In case of high potent drugs,
it is much easier to contain a
roller compactor than a fluid bed
dryer. One has to point out that
in the past decade, equipment
manufacturers have introduced
more instrumentation and advanced
control systems, such as Gerteis or LB
Bohle to name a few, allowing a more
consistent ribbon density through a
gap control loop system acting on the
feeding rate.
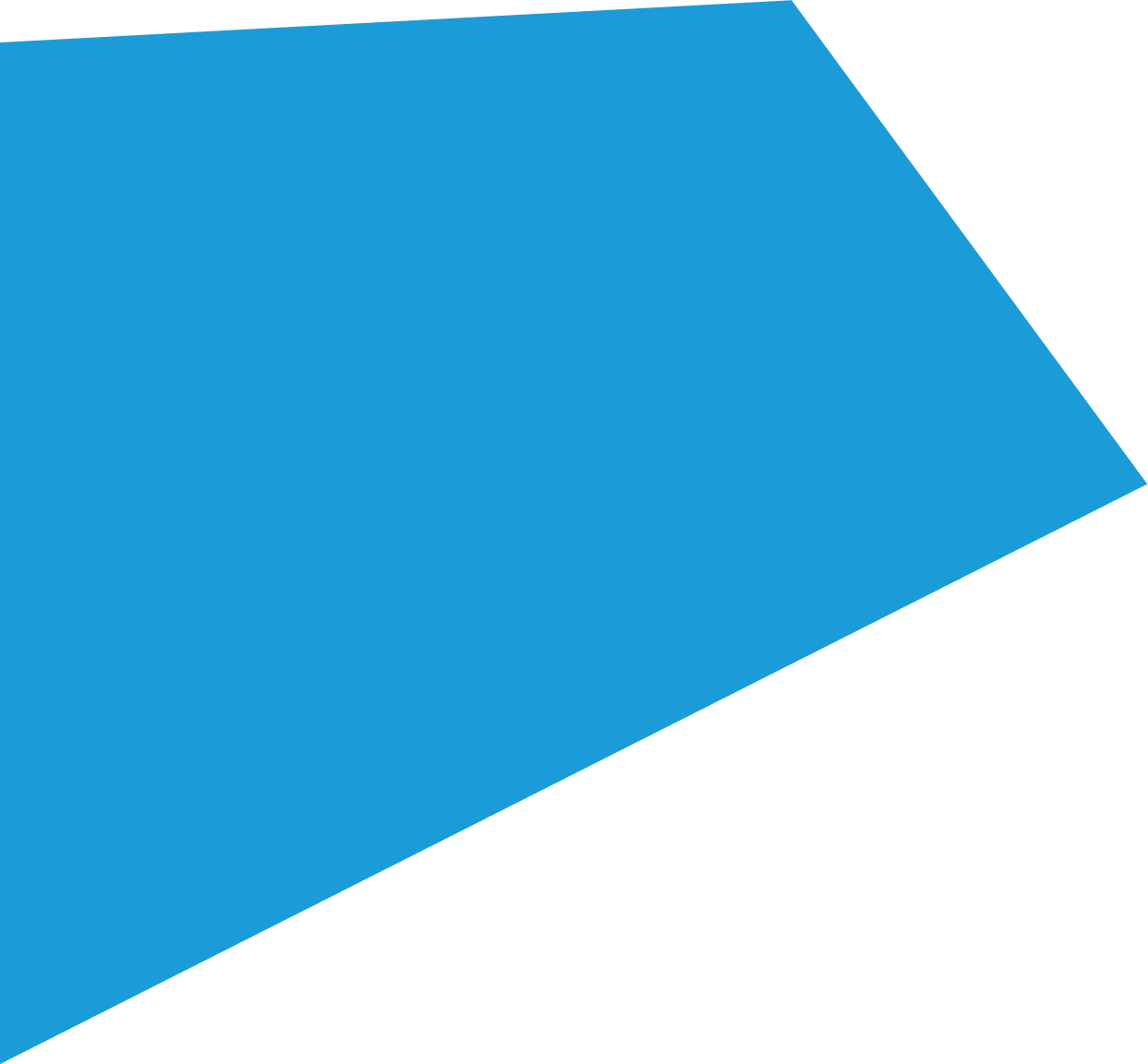
WHICH SOLUTIONS EXIST TODAY
TO SCREEN FORMULATIONS FOR THEIR
SUITABILITY TO DRY GRANULATION?
Formulation scientists have to
screen several formulas to ensure
proper Quality Attributes, such as
tablet breaking force, disintegration
time and dissolution profiles. R&D
roller compactors have usually large
rolls, which means that the required
quantity of API to run a test is fairly
high, a main hurdle at the early stages
when the API is not available in large
quantity, not to mention the cost per
kilo. One solution could have been to
use a roller compactor with small rolls
in order to use a smaller quantity of
material. However, these small rolls
cannot achieve the densification of
large rolls used in production and
this can yield to false negatives when
considering the material ability to
be dry granulated. That is the reason
why people are looking for alternative
methods to assess the feasibility of
dry granulation in the early stages of
the development.
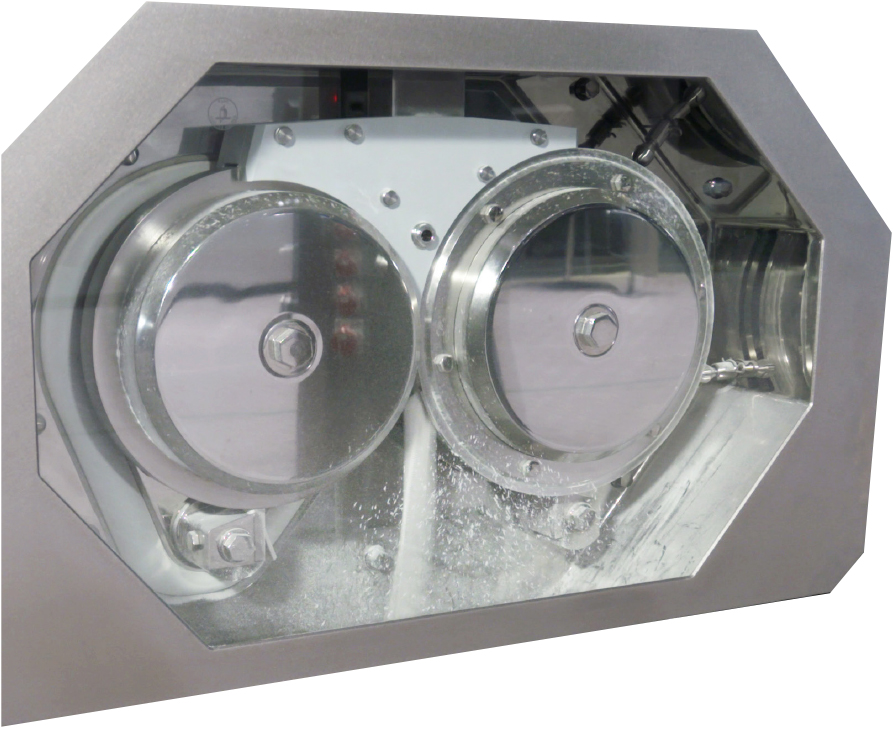
Roller Compactor
CAN YOU DESCRIBE IN MORE DETAILS
THIS MATERIAL SPARING METHOD?
This method was introduced
back in 2004 in a publication
from Pfizer [1] in the USA. Their
proof of concept was to show that
density-pressure plots were identical
between compacts made on a single
punch press and ribbons made on
real roller compactor. Both punches
on the single punch press, a “roller
compaction simulator” to be precise,
was following a sine-wave path to
mimic the compression dynamics
occurring between the rolls of roller
compactors. The rolls diameter and
rolls speed were taken into account
to be as close as possible to the
production process.
To be more precise, the relative
density, also called solid fraction,
was used instead of the density. This
solid fraction is calculated by dividing
the ribbon density by the powder
true density, a parameter generally
measured with a helium pycnometer.
Solid Fraction =
It is important to note that the
pressure measured on a single punch
press is not directly comparable with
the pressure on a roller compactor.
Back in 2004, Pfizer just manually
fitted the compressibility curves
together to have a correlation
between the pressures on both
equipment units
Density
Powder true density
This method was introduced
back in 2004 in a publication
from Pfizer [1] in the USA. Their
proof of concept was to show that
density-pressure plots were identical
between compacts made on a single
punch press and ribbons made on
real roller compactor. Both punches
on the single punch press, a “roller
compaction simulator” to be precise,
was following a sine-wave path to
mimic the compression dynamics
occurring between the rolls of roller
compactors. The rolls diameter and
rolls speed were taken into account
to be as close as possible to the
production process.
To be more precise, the relative
density, also called solid fraction,
was used instead of the density. This
solid fraction is calculated by dividing
the ribbon density by the powder
true density, a parameter generally
measured with a helium pycnometer.
Solid Fraction =
Density
Powder true density
It is important to note that the
pressure measured on a single punch
press is not directly comparable with
the pressure on a roller compactor.
Back in 2004, Pfizer just manually
fitted the compressibility curves
together to have a correlation
between the pressures on both
equipment units
Density
Powder true density
This method was introduced
back in 2004 in a publication
from Pfizer [1] in the USA. Their
proof of concept was to show that
density-pressure plots were identical
between compacts made on a single
punch press and ribbons made on
real roller compactor. Both punches
on the single punch press, a “roller
compaction simulator” to be precise,
was following a sine-wave path to
mimic the compression dynamics
occurring between the rolls of roller
compactors. The rolls diameter and
rolls speed were taken into account
to be as close as possible to the
production process.
To be more precise, the relative
density, also called solid fraction,
was used instead of the density. This
solid fraction is calculated by dividing
the ribbon density by the powder
true density, a parameter generally
measured with a helium pycnometer.
Density
Powder true density
Solid Fraction =
Density
Powder true density
Destiny
Powder true density
It is important to note that the
pressure measured on a single punch
press is not directly comparable with
the pressure on a roller compactor.
Back in 2004, Pfizer just manually
fitted the compressibility curves
together to have a correlation
between the pressures on both
equipment units
Powder true density
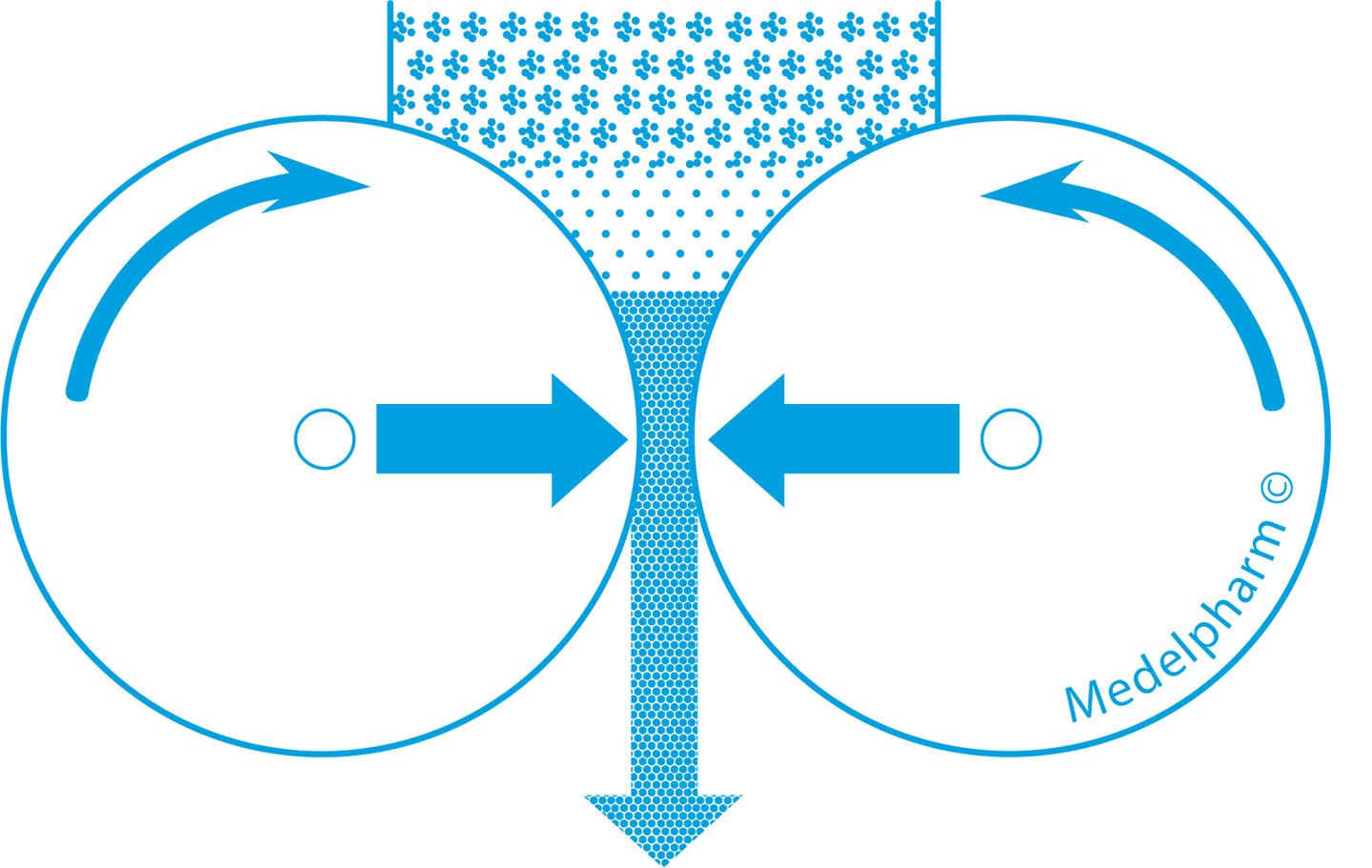
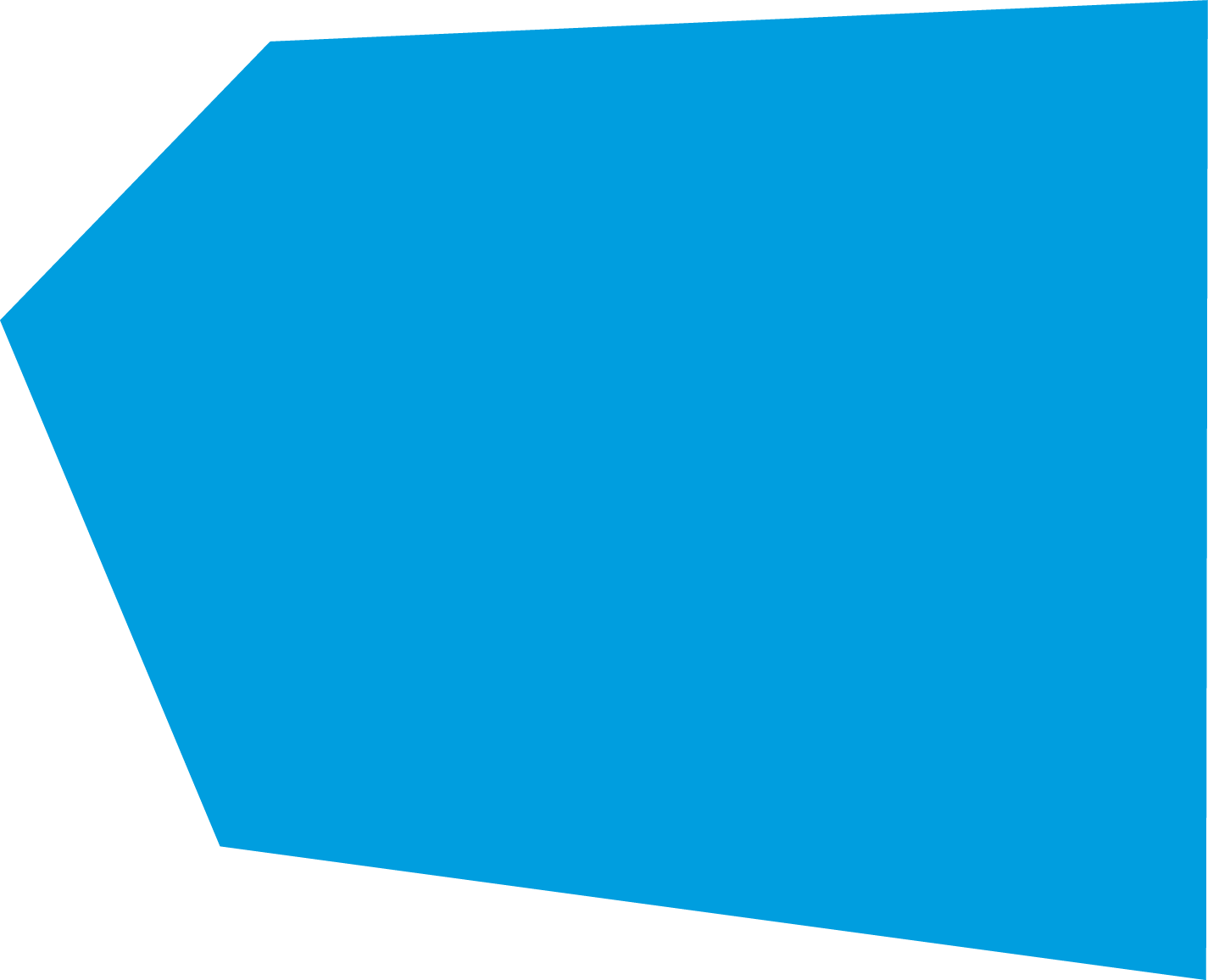
HOW DO YOU PROVE THAT THIS
METHOD GIVES SIMILAR RESULTS
AS ON A ROLLER COMPACTOR?
F
irst, like any material-sparing
methods, mimicking the dry
granulation process on a single punch
press has some limitations. The
feeding system, de-aeration, pressure
gradient along the ribbon width, the
roll surface and shape are actually
not taken into account. That’s sounds
like a lot, but this method is actually
the only method to evaluate the dry
granulation process at early stages.
The dry granulation is a slow
symmetric compaction process. Many
formulators were using eccentric
presses trying to predict the powder
ability to be dried granulated
with more or less success, as this
compaction is asymmetric and
therefore does not fully mimic a roller
compactor.
More recently Sanofi published
research performed on a Medelpharm
rotary press simulator at very slow
speed with the benefit of symmetric
compaction. Their findings were
already much more satisfactory. [3]
With the new STYL’One Tableting
Instrument, this method was greatly
improved. This was achieved by
implementing a mathematical model
to compute, from the pressure
measured on the STYL’One, the
equivalent hydraulic pressure (or
specific compaction force) that should
be entered on a roller compactor to
reach the same solid fraction. This
method is called “hybrid modelling”,
since it uses a mathematical model
combined with real compacts made
on a single punch press. Recently, the
University of Düsseldorf published a
paper [2] using different excipients
(brittle, plastic). They've shown that
compacts, called ribblets (a neologism
created from ribbon + tablet) made
on a STYL'One and ribbons made on
a Gerteis roller compactor had similar
relative density.
Even with the limitations listed
earlier, this material-sparing method
remains the most effective method
available to assess dry granulation
with a small amount of material. It
has been adopted by pharmaceutical
companies across the globe as one
of their reference method to decide if
dry granulation is a feasible process
and to speed up their design of
experiments (DoE) when scaling-up to
a commercial-size roller compactor.
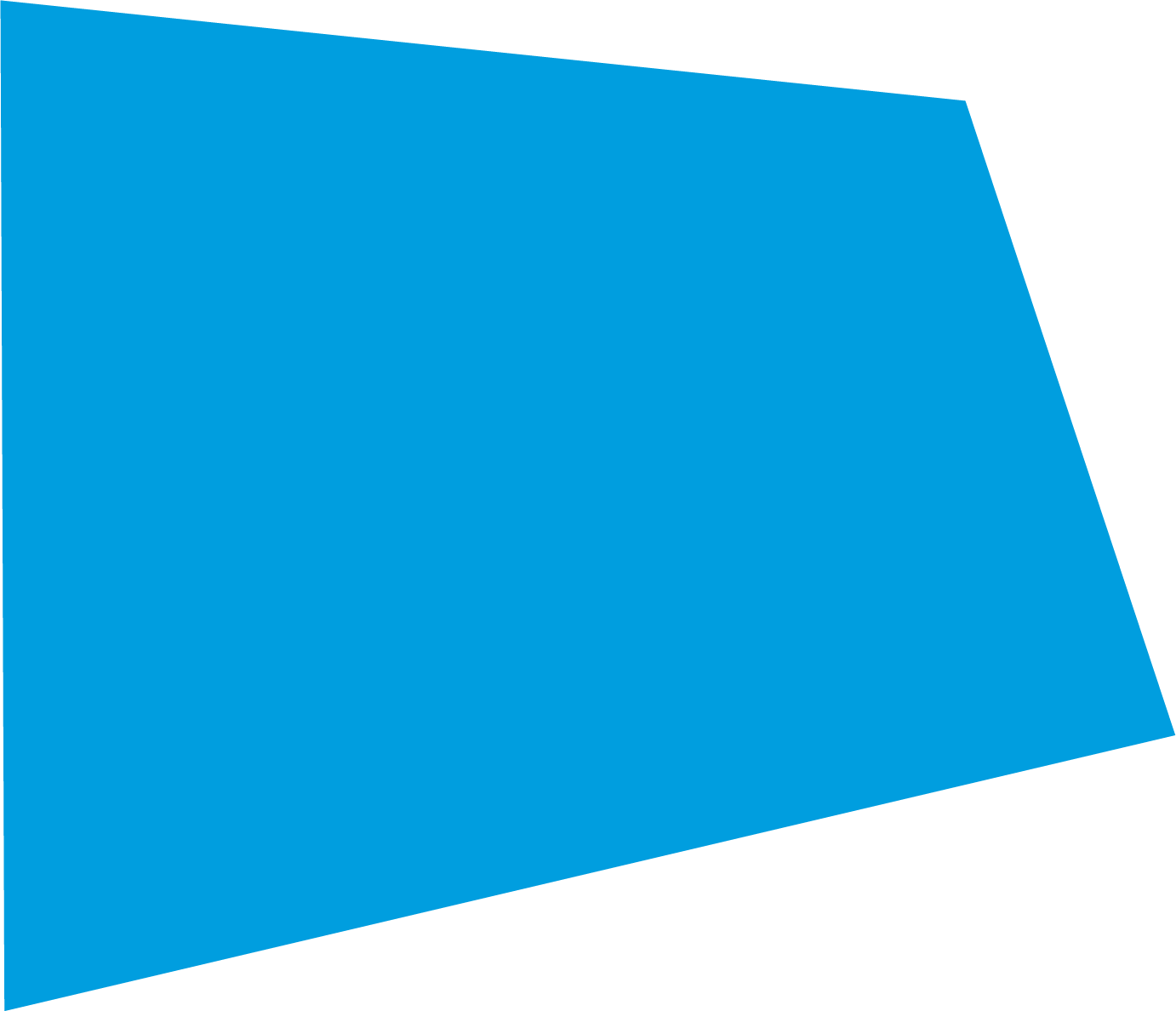
WHAT ARE THE BENEFITS OF USING
STYL'ONE TABLETING INSTRUMENT TO
ASSESS A DRY GRANULATION PROJECT?
The philosophy of STYL’One is
to help formulation scientists
to easily implement this method,
which is integrated in the software
controlling the press. The formulator
can choose from a library of branded
roller compactors, such as Gerteis,
LB Bohle, Fitzpatrick, Alexanderwerk,
Vector-Freund, Hosokawa Bepex.
Each profile bears all the physical
characteristics: roll diameter and
width, roll speed, gap range, specific
compaction force or hydraulic
pressure. Ribblets can be produced
in a desired thickness (gap) and
pressure. If the True Density is known,
the operator can simply select a
desired Solid Fraction, typically
between 0.6 and 0.8, and a thickness
(gap) and STYL'One make the ribblets
within specifications.
The key benefit of this method
is the use of an extremely small
quantity of API at the early stage of
development.The formulator can
design a small DoE with, for instance,
3 solid fractions at the same gap
and different formulations. Then,
make a few ribblets, mill them to
obtain dry granules, and recompress
them into tablets, which can be
characterized with tablet breaking
force, disintegration time and
dissolution profiles. All of this will help
the selection of the right formulation.
This method saves time and mitigates
the risks of scale-up to a real roller
compactor. It allows you to select the
most adequate formulation and gives
good approximation of the process
parameters to be used on the roller
compactor to achieve the desired
Quality Attributes.
[1] Zinchuk, Andrey V., Matthew P. Mullarney, and Bruno C. Hancock.
“Simulation of Roller Compaction Using a Laboratory Scale
Compaction Simulator.” International Journal of Pharmaceutics 269,
no. 2 (January 2004): 403–15.
https://doi.org/10.1016/j.ijpharm.2003.09.034.
[2] Reimer, Hannah L., and Peter Kleinebudde. “Hybrid Modeling of Roll
Compaction Processes with the STYL’One Evolution.”
Powder Technology, February 2018.
https://doi.org/10.1016/j.powtec.2018.02.052.
[3] Bardet, Lionel. “Compression Simulator (Stylcam) as a Modeling
Tool for Roller Compaction Process.” presented at the Journée
d’information APGI, Lyon, October 15, 2013.
http://www.tablet-tech.com/slides.